نگاهی به کمپرسورها
امروزه یکی از ارزانترین ، پاک ترین، راحت ترین و در دسترس ترین انرژی های جهان ، انرژی هوای فشرده است که بشر همواره به دنبال استفاده از این نوع انرژی جهت استفاده در صنایع مختلف تولیدی اعم از صنایع غذایی – پتروشیمی – پالایشگاه ها – فولاد – داروسازی – خودروسازی - صنایع دفاع و ... بوده است.
به دلیل اهمیت کاهش هزینه ها در تولید و نقش بسزای آن در رقابت بین شرکتها و حتی در بین کشورهای تولید کننده ، ضروری است از انرژی هایی که محرک اصلی کارخانجات میباشد استفاده کنیم که اولا ارزان قیمت و به راحتی قابل دسترس باشد.
ثانیا از نظر سرعت عمل کاری و مهمتر از همه ، از نظر راندمان کاری بتواند برای یک شرکت مقرون به صرفه باشد.
راندمان نشان دهنده جلوگیری از هدر رفتن مواد – سرمایه – زمان – انرژی در انجام کارها است.
راندمان معمولا بصورت نسبت (خروجی مفید) به (ورودی کل) تعریف و محاسبه میشود.
کمپرسور:
یک ماشینی است که کار اصلی آن متراکم ساختن سیال هوا را به عهده دارد طوری که هوا را در یک یا چند مرحله متراکم ساخته و در یک مخزن که اصطلاحا رسیور تانک (receiver tank) نیز میگویند، ذخیره ساخته و هوای فشرده پس از فیلتر شدن (حذف بخار روغن و رطوبت هوا ) توسط مدار لوله کشی شده به سالن تولید هدایت میشود.
تکنولوژی هوای فشرده
هوای فشرده یک منبع انرژی پنوماتیکی است که مانند انرژی الکتریکی و هیدرولیکی در بخشهای مختلف تولید اکثر صنایع کاربرد دارد علاوه بر آن کاربردهای دیگری نیز مانند تولید بطری های پلاستیکی (پت) ، راه اندازی تجهیزات دوار سنگین ، تست نشتی تجهیزات پنوماتیکی و ..... را شامل میشود
کلیه تجهیزاتی که با مصرف یک صورت از انرژی و تبدیل آن به یک صورت انرژی دیگر از طریق چرخش محور تجهیزات کار میکنند تجهیزات دوار نامیده میشوند مانند موتور های احتراقی ، پمپ ها ، الکترو موتورها و کمپرسورها.
کمپرسور ها (فشرده کننده ) نوعی از تجهیزات دوار است که برای فشرده سازی ، به جریان انداختن و افزایش فشار گاز ها برای دستیابی به اهداف مورد نظر اطلاق می شود.
کمپرسور هارا می توان به شکل زیر دسته بندی نمود :
کمپرسورها ( Compressors) :
بنا به تعریف کمپرسور ها برای فشردهسازی انواع گاز ها طراحی و ساخته میشوند. از آنجایی که روغنکاری قطعات درگیر باهم در حین کار کمپرسور ضروری است و از سویی اختلاط و یا عدم اختلاط گاز فشرده شده با روغن اهمیت دارد نحوه روغنکاری کمپرسور نیز اهمیت پیدا میکند.
در صنایعی مانند صنایع دارویی ، پتروشیمی ، غذایی و .... گاز فشرده شده به روغن حساسیت دارد و نباید با روغن مختلط شود در این صنایع از کمپرسور های Oil Free ( خشک ) استفاده میشود طراحی این دستگاه ها بنحوی است که در محفظه تراکم هیچ روغنی وجود ندارد.
امروزه غیر از موارد اجباری مانند موارد بالا حتی الامکان سعی میشود از کمپرسور های خشک استفتده نشود . کمپرسورهای خشک هر چند از نظر کاربردی ضروری است ولی به لحاظ قیمت بالاتر ، هزینه های تعمیر نگهداری بیشتر ، پایین بودن راندمان ، قابلیت اعتماد کمتر و ... قیمت تمام شده محصول تولیدی را بالا می برند. در طراحی این کمپرسور ها جهت کاهش اثرات این مشکلات استفاده از مواد با کیفیت بالا ، ضد سایش و نوع روانکاری مدنظر است.
در کمپرسور های رفت و برگشتی اختلاط روغن با گاز مورد تراکم ناخواسته و از طریق نشت روغن به محفظه تراکم صورت میگیرد.
در کمپرسور های چرخشی مانند کمپرسور های Screw (پیچی ) اختلاط روغن با گاز مورد تراکم عمدا صورت میگیرد در این کمپرسور ها روغن تحت فشار گاز در محفظه تراکم با گاز مورد تراکم اختلاط یافته و عملیات روانکاری ، خنک کاری و کاهش نشتی گاز از طریق لقی موجود بین قطعات را انجام میدهد سپس روغن در قسمت Separator (جدا کننده ) از گاز جدا شده و بعد از خنک کاری به مخزن مربوطه سیرکوله میشود.
امروزه کمپرسور های Screw با توجه به مزایای آن ( قیمت مناسب ، هزینه نگهداری کمتر و راندمان بیشتر ) در اکثر صنایع جایگاه خوبی یافته و استفاده از آن روز به روز بیشتر میشود.
طرز کار کمپرسور Screw :
قلب اصلی این کمپرسور ها واحد هواساز که دارای دو عدد روتور مارپیچی با پروفایل های متفاوت بوده که توسط الکتروموتور چرخانده میشود.
در مرحله اول با چرخش روتورها هوا و روغن به فضای بین پره روتور ها مکیده شده و با ادامه چرخش روتور ها فشار هوای محبوس شده با کاهش حجم آن افزایش می یابد روغن در این مرحله نقش روانکاری و خنک کاری روتور ها و واحد هواساز را بر عهده دارد . این کم شدن حجم تا قسمت تخلیه هوا ادامه یافته تا فشار به حد دلخواه برسد.
در مرحله بعد هوای فشرده شده در قسمت Separator از روغن جدا شده و پس از خنک کاری به مخزن ذخیره هوای فشرده جریان مییابد و همچنین روغن نیز پس از خنک کاری به مخزن مربوطه سیرکوله میشود.
فشار تولیدی در این کمپرسور ها حداثر تا 13 بار است و مقدار هوادهی ( دبی ) تا بیشتر از 50m3/min (50 متر مکعب در دقیقه) نیز میرسد. رجوع شود به کاتالوگ کمپرسور های Screw TCP S & TCP SD series
بوسترها :
همانطوری که اشاره شد فشار هوای تولیدی کمپرسور های اسکرو حداکثر تا 13 بار است که این مقدار فشار در اکثر صنایع مطلوب است در بعضی صنایع مانند تولید بطری ها و ظروف پلاستیکی (پت) نیاز به فشار تا 40 بار میباشد که برای این منظور از بوستر استفاده میشود.
بجای طراحی سیستم های بزرگ و کامل با فشار بالای مورد نظر در صنایع مذکور افزایش فشار هوای فشار پایین تا سطح فشار مورد نیاز مناسب ترین راه حل بوده و بوستر ها بدن منظور طراحی و ساخته میشوند.
بوستر در حقیقت یک نوع از کمپرسور های رفت و برگشتی است که توسط الکترو موتور پیستون ها در داخل سیلندر به حرکت در می آیند و نحوه عملکرد آن به این صورت میباشد که هوای کم فشار تولید شده در کمپرسور های اسکرو به داخل محفظه تراکم بالای پیستون ها هدایت شده و با کاهش حجم آن، فشار افزایش یابد و پس از خنک کاری به مخزن ذخیره فشار بالا هدایت میشود.
شایان ذکر است هوادهی ( دبی ) بوستر ها در مقادیر کم مورد نیاز است و از این نظر استفاده از بوستر کاملا اقتصادی و مقرون بصرفه است ( رجوع شود به کاتالوگ بوستر ها )
کمپرسور های فشارقوی :
کمپرسور های فشار قوی از نوع کمپرسور های رفت و برگشتی پیستونی دو مرحله ای بوده که در پیستون های مرحله اول هوای فشار کم تولید و به بالای پیستون های مرحله دوم ارسال میشود و با حرکت پیستون ها حجم هوای مذکور کاهش و فشار آن افزایش می یابد.دبی این کمپرسور ها نیز در مقادیر کم بوده و جهت راه اندازی تجهیزات دوار سنگین و مخصوصا تجهیزات صنایع دریایی کاملا مفید و اقتصادی است. ( رجوع شود به کاتالوگ کمپرسور پیستونی قشار قوی )
درایر ها ( Dryers ) خشک کن ها :
از آنجاییکه هوای محیط مرطوب و غبار آلود بوده و رطوبت پس از فشرده سازی بصورت بخار آب در می آید و در مواقع مصرف ممکن است مشکل ایجاد نماید از وسایلی بنام درایرها و تله آبگیر ها و میکروفیلتر ها استفاده میشود . تله آبگیر و درایر بعد از مخزن هوای فشرده بهمراه میکرو فیلترها کار گذاشته میشود و وظیفه این دستگاه ها گرفتن بخار و رطوبت هوای فشرده شده و تخلیه آن به بیرون است.
جهت گرفتن غبار هوای فشرده از Dust filter ( فیلتر غبار گیر ) استفاده میشود.
شایان ذکر است در مصارف عمومی(General applications )که بخار و گرد و غبار موجود مشکل ایجاد ننماید میتوان مستقیما از مخزن استفاده نمود.
معمولا میزان فشار لازم در صنایع مختلف 7-13 bar میباشد که عمده صنایع مختلف از فشار کاری 7 bar یا 8bar استفاده می کنند.
لازم به ذکر است کمپرسورها از نظر دسته بندی ( نوع ) در گروه های ذیل تقسیم بندی میشوند.
1 -کمپرسورهای جابجایی مثبت
کمپرسور پیستونی کمپرسور اسکرو
2 -کمپرسورهای گریز از مرکز
کمپرسورهای توربینی
کاربرد کمپرسورها در صنایع مختلف
کلا در انتخاب کمپرسور به دو مورد فشار کاری و حجم هوای فشرده بایستی توجه کرد.
معمولا در صنایع کوچک از کمپرسورهای پیستونی استفاده میشود.
این نوع کمپرسورها معمولا تا فشار کاری 8 بار و حجم هوای تا 1500 لیتر بر دقیقه کار میکنند.
الکتروموتور مورد استفاده شده در این کمپرسورها معمولا 1.5kw تا 7.5kw است.
در صنایعی که حجم هوای خیلی زیاد مورد نیاز میباشد معمولا از کمپرسورهای اسکرو استفاده میکنند و معمولا الکتروموتور استفاده شده در این نوع کمپرسورها از 7.5kw تا 315kw و همگی سه فاز هستند.
لازم به ذکر است الکتروموتورها را معمولا بر حسب اسب بخار ( با علامت ( hpیا کیلو وات ( با علامت kw ) میگویند.
Hp=1.341*kw
نمایی از کمپرسور اسکر
سیستم اسکرو
نمای داخلی یک کمپرسور اسکرو که به صورت کوپل مستقیم میباشد
جدول انتخاب کمپرسورهای اسکرو نسبت به حجم (دبی) و فشار مورد نیاز
در صنایع مانند فولاد – شیشه – پالایشگاه ها – پتروشیمی که در آن حجم هوای بسیار بالایی مورد نیاز است بایستی از کمپرسورهای متعدد با سایز بالا یا از کمپرسورهای سانترفیوز (گریز از مرگز) استفاده نمود.
حداکثر حجم تولید هوای فشرده در سیستم های اسکرو تا 53m3/min است ولی حداقل حجم تولید هوای فشرده در سیستم های سانترفیوژ از 80m3/min شروع می شود.
یک نمونه از دستگاه کمپرسور با سیستم سانترفیوژ
نحوه ورود هوای اتمسفر به توربین و فشرده سازی
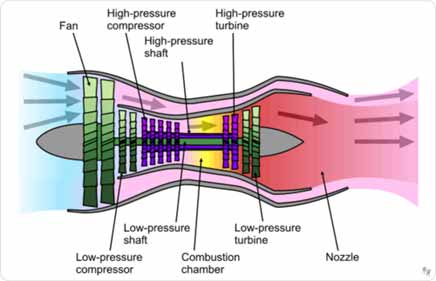
فیلتراسیون هوای فشرده
هوایی که تنفس میکنیم طبیعتا دارای رطوبت است. حال فرض کنیم این هوای فشرده که تنفس میکنیم ، توسط کمپرسور آن را فشرده کنیم ( متراکم کنیم و فشار آن را بالا ببریم )و داخل یک مخزن ، ذخیره می کنیم.
همان رطوبتی که همراه هوای معمولی است نیز به صورت حجم بالا همراه هوای فشرده داخل مخزن ذخیره می گردد.
یکی از آسیبها و ضررهای مالی که صنایع بعضا در بخش تولید و ماشین آلات متحمل میشوند ، خرابی جکهای پنوماتیکی – شیر برقی ها – زنگ زدگی لوله ها انتقال هوای فشرده – خرابی یا معیوب شدن محصول تولیدی بر اثر برخورد رطوبت هوا و ... است. ( مانند ظروف شیشه ایی و پلاستیکی )
برای جلوگیری و کاهش این آسیبها بایستی هوای خروجی از کمپرسور را فیلتر کنیم طوری که میزان رطوبت آن به حداقل ممکن برسد. برای این منظور دستگاه درایر تبریدی یا درایر جذبی را در مسیر هوای فشرده تعبیه میکنند تا رطوبت را از هوا جدا کرده و هوای خشک و سالم به سمت سالن تولید هدایت شود.
رطوبت گیری توسط دستگاه درایر که به دو نوع تبریدی و جذبی تقسیم می شوند ، انجام می گیرد.
در سیستم تبریدی ، هوا وارد مبدل حرارتی شده و با توجه به ایجاد نقطه شبنم در داخل آن ، عمل کندانس انجام شده و رطوبت گیری توسط سیکل تبرید تراکمی تکمیل می شود.
در زیر سیکل تبرید و سیکل رطوبت گیری نشان داده می شود.
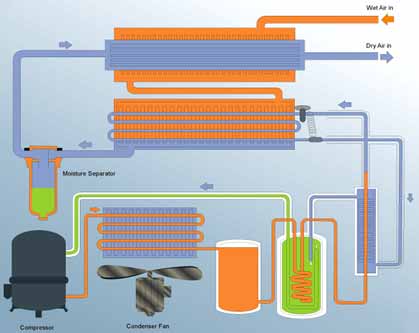
درایر جذبی
در سیکل رطوبت گیری درایر جذبی ، مواد جاذب رطوبت که عمدتا در سه نوع آلومینیوم اکتیو ، مولکولارسیو ، سلیکاژل میباشند در برجکهای دستگاه قرار گرفته و در هنگام عبور هوای فشرده از برجکها ، این مواد رطوبت موجود در هوا را گرفته و هوای خشک به سمت مصرف هدایت می شود.
طراحی این سیستم طوری میباشد که نسبت به تعریف مدت زمان خاص ، شیرهای راه دهنده پنوماتیکی اقدام به تعویض مسیر هوای عبوری از یک برجک به برجک دیگر میشود.
درایر های جذبی و تبریدی کاربردهای خاص در مکانهای خاص دارد به این معنی که در هر جایی نباید از هر درایری استفاده کرد یا بهتر بگوییم ، شرایط جغرافیایی دمای شبنم ، حجم و دبی کمپرسور هوا تعیین کننده انتخاب نوع درایر است و در صورت عدم انتخاب مناسب میتواند باعث کاهش راندمان و هدر رفت انرژی و افزایش هزینه ی تولید گردد که در فصل های آینده به طور مفصل به این قضیه خواهیم پرداخت.
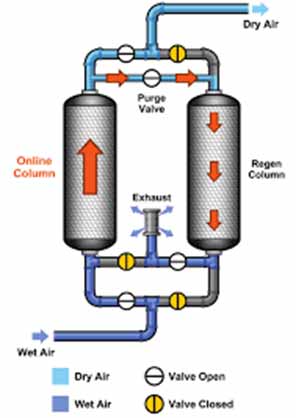
دستگاه درایر جذبی
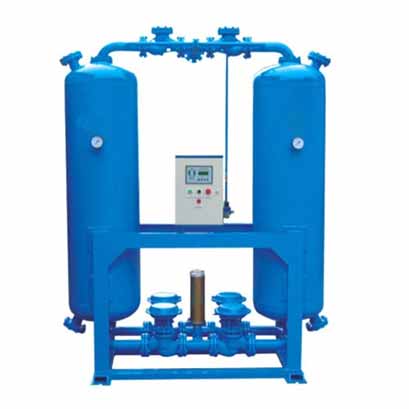
نگاهی به راندمان و اهمیت آن در صنعت
در فصل قبل به صورت مختصر با کمپرسورهای هوای فشرده و همچنین سیستم فیلتراسیون یا همان تجهیزات جانبی کمپرسورها آشنا شدیم و هدف از نوشته های قبلی ، آشنایی با اهمیت انتخاب صحیح تجهیزات و ... بود.
در این فصل نگاهی خواهیم انداخت به این مسئله که چرا بایستی تجهیزات تاسیسات اعم از کمپرسور و دستگاههای فیلتراسیون و ... درست انتخاب شوند و یا اینکه کوچکترین و جزئی ترین ایرادات ممکن در دستگاه ها و حتی مسیر هوای فشرده چه هزینه های گزافی را به تولید کننده وارد می کند.
در فصل های بعد راجع به راندمان بحث مفصلی خواهیم داشت البته از بعد فنی و ریز به ریز مسائل فنی و تا جایی که امکان دارد را بررسی خواهیم کرد(با ذکر جداول و نمودارهای مربوط به کمپرسور و تجهیزات جانبی )
اما قبل از بررسی خود دستگاه کمپرسور و اینکه چه راه هایی را میتوانیم ارائه کنیم تا بتوانیم راندمان کمپرسور را بالا ببریم ، لازم است در مورد انتخاب دستگاه ها مواردی را اشاره کنیم و این مورد را بررسی خواهیم کرد که آیا یک انتخاب خوب در خرید ماشین آلات هوای فشرده میتواند به افزایش راندمان کمک بکند یا نه؟
برای ساده تر شدن مسئله یک مثال میزنیم:
فرض کنیم یک کارخانه لبنیات به 12m3/min هوای فشرده با فشار کاری 7barنیاز دارد (لازم به ذکر است ، مجموعه دستگاه های مورد استفاده ، جمعا 12m3/min هوای خالص نیاز دارند)
لازم به ذکر است که در انتخاب کمپرسور به چند آیتم باید توجه شود:
- منطقه جغرافیایی
- ارتفاع تقریبی
- دمای تقریبی مکان مورد استفاده
- رطوبت تقریبی منطقه
منظور از منطقه جغرافیایی این است که دستگاه در مکانهایی مانند کنار دریا – سکوهای نفتی است یا در جاهای معمولی مثل شهرکهای صنعتی.
آیتم ارتفاع بسیار مهم است .همانطور که میدانیم هر چقدر از سطح آبهای آزاد بالاتر برویم هوا رقیقتر خواهد بود یا به زبان ساده به علت کاهش فشار ، فاصله ی مولکولهای هوا از هم بیشتر میشود و در نتیجه حجم هوا کاهش پیدا می کند.
به عبارتی دیگر اگر در کنار آبهای آزاد که فشار هوا یا اتمسفر برابر با 1bar یا معادل 14.7psi باشد را ضریب یک در نظر بگیریم با افزایش ارتفاع ، این ضریب کاهش پیدا میکند و در معادلات مربوط به محاسبات حجم هوا توسط کمپرسور بایستی اعمال شود.
به عنوان مثال ارتفاع شهر تبریز از آبهای آزاد 1260 متر میباشد که طبق نمودار ( ص ...) تقریبا ضریب ./85 را در معادلات قرار می دهیم.
آیتم رطوبت را معمولا 50% در نظر می گیرند.
نمودار ارتفاع و ضریب هوادهی
انتخاب کمپرسور:
همان کمپرسور 90kw را در نظر می گیریم
اگر کارخانه ایی را در نظر بگیریم که نیاز به هوای فشرده 12m3/min داشته باشد و اقدام به خرید یک دستگاه 90kw نماید و همان دستگاه اگر به هر دلیلی ایراد پیدا کند ، کل کارخانه و تولید تعطیل خواهد شد و تعطیلی یک واحد خسارت جبران ناپذیری را به بار خواهد آورد. پس در اینجا میبینیم خرید یک دستگاه معقول نیست و بهتر است در این مواقع دستگاه کوچکتر با تعداد بیشتر خریداری گردد.
مزایای استفاده از کمپرسورهای مکرر:
1: اگر یک دستگاه ایراد پیدا کند ، کل واحد تولیدی تعطیل نمیشود و مدیر تولید نسبت به اولویت و حساسیت کار یک بخش جز را تعطیل میکند.
2: میتوانیم سالن تولید را نسبت به تعداد کمپرسورها منفک کنیم.
حال ببینیم در عمل ، خرید کمپرسورهای کوچک با تعداد بالا چگونه است.
از جدول (....) مشخصات کمپرسور 90kw با فشار کاری 7bar را می آوریم:
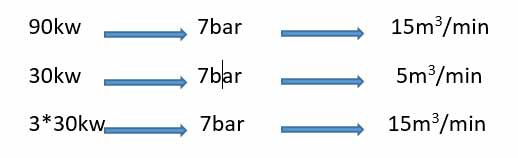
پس نتیجه میگیریم داشتن کمپرسورهای متعدد نه تنها هزینه ی اضافه به تولید کننده تحمیل نمیکند بلکه در مواقع اضطراری مانع از توقف تولید میشود و حتی میتوانیم بگوییم در بعضی مواقع در مصرف هزینه نیز صرفه جویی می شود.
فرض کنیم تعدادی از دستگاههای یک تولیدی بر اثر نبود مواد اولیه -تعمیر و نگهداری و ... متوقف میشوند و در این هنگام یکی از کمپرسورها خاموش شده و بر حسب نیاز کمپرسورهای دیگر در مدار خواهند بود.
لازم به ذکر است اگر در شرایط یکسان (کاهش مصرف هوای فشرده ) هر دو سیستم را از نظر مصرف انرژی بررسی کنیم داریم:
تعداد یک کمپرسور 90kw در حالت کار 153 آمپر جریان مصرفی دارد در حالی که حتی قسمت خیلی جزیی از خط تولید کار کند همین کمپرسور 90kw باید کار بکند ولی اگر تعداد کمپرسور (30kw*2) باشد ، جریان مصرفی 102 A خواهد بود.یک مسئله بسیار مهم که باید به آن توجه کنیم این است که هر الکتروموتور در لحظه استارت اولیه ، سه برابر آمپر مجاز جریان مصرفی خواهد داشت یعنی یک کمپرسور 90kw که در آن یک دستگاه الکتروموتور 90kw در آن قرار دارد ، به هنگام استارت حدود 459 A در سه ثانیه اول جریان خواهد کشید ولی دو دستگاه کمپرسور در مجموع و در حالتی که فرض کنیم هر دو کمپرسور باهم استارت زده می شوند مقدار 306A در سه ثانیه اول جریان خواهند داشت.
شاید فکر کنیم یک کمپرسور 980kw اگر با ظرفیت 50% کار کند به حد کافی هوای فشرده را در مخزن ذخیره خواهد کرد و زمان استراحت کمپرسور افزایش پیدا خواهد کرد در حالی که به اعضای هر استارتی که زده میشود معادل 459A در سه ثانیه اول جریان برق مصرف خواهد کرد که یک هزینه سر سام آور را به تولید تحمیل میکند بعلاوه اینکه چون در لحظه ی استارت ، یکدفعه این مقدار جریان را از مدار مصرف میکند ممکن است آسیب زیادی به سایر دستگاه های موجود در تاسیسات یا خط تولید صدمه وارد نماید.
گاها ، تولید کننده برای جلوگیری از این مشکل مجبور است با صرف هزینه زیاد نسبت به نصب بانک خازن نماید.
( بانک خازن جهت ذخیره برق و جلوگیری از نوسان و تخلیه یکباره جریان در مدار است)
نگاهی به راندمان
در فصل گذشته نگاهی گذرا به کمپرسورهای هوای فشرده و تجهیزات فیلتراسیون داشتیم.هدف از نگارش فصل قبل ، آشنایی با نحوه ی کار کمپرسور و انواع آن و نقش مهم آن در صنایع مختلف و همچنین اهمیت تجهیزات فیلتراسیون بعد از کمپرسور بود.
همچنین نگاهی داشتیم به نحوه ی انتخاب کمپرسور در یک واحد تولیدی و اینکه یک انتخاب کارشناسی و مناسب چقدر می تواند هزینه های جانبی یک واحد تولیدی را کاهش دهد.
در این فصل نگاه مفصلی خواهیم داشت به بحث راندمان و اینکه چگونه می توانیم حدالمکان بتوانیم راندمان کمپرسورها را افزایش دهیم.
باید توجه داشت در بحث افزایش راندمان کمپرسور فقط نباید دنبال راهی باشیم یا دنبال یک تکنولوژی خاصی برویم که راندمان را افزایش دهیم بلکه باید بدانیم حتی انتخاب صحیح کمپرسور در یک واحد تولیدی نوعی افزایش راندمان است.
پس در مرحله ی اول با انتخاب کارشناسی ، قدم اول را خواهیم برداشت ، در صورت عدم رعایت این موارد نه تنها با مشکلات زیادی مواجه خواهیم بود بلکه در مسیر خلاف قدم بر میداریم.
لازم به ذکر است به صورت نرمال در بحث راندمان میتوانیم سهم افزایش راندمان را به دو قسمت تقسیم کنیم
سهم اول خریدار
سهم دوم تولید کننده کمپرسور و طراح
همانطور که در فصل قبل نیز اشاره شد در مورد انتخاب صحیح کمپرسور بایستی دقت کافی داشته باشیم.
چون هدف ما از افزایش راندمان ، کاهش مصرف انرژی یا بهتر است بگوییم جلوگیری از هدر رفت انرژی و بدنبال آن کاهش هزینه هااست.
قبل از خرید حتما باید از مشاوره های فنی افراد شناخته شده استفاده گردد چون ماشین آلات تاسیسات پیچیدگی های خاص خود را دارند و در مورد انتخاب آنها نیاز به مهارت و دانش خاص خودشان را دارد و این موردی است که افراد با تجربه میتوانند به کارفرما کمک کنند.
افزایش راندمان در کمپرسور در دو قسمت برق و مکانیک اتفاق می افتند یعنی بایستی کارهایی را در این قسمتها انجام دهیم که موجب افزایش راندمان شود.
در این بخش به بررسی و و عملکرد دستگاههای سافت استارتر و اینورتر و تاثیر آن در مصرف انرژی کمپرسور خواهیم پرداخت.
تفاوت سافت استارتر و اینورتر
در مورد فرق این دو باید گفت که سافت استارتر همانطور که از اسمش پیداست راه انداز نرم موتور هست که از ایجاد تنش های مکانیکی روی موتور وبلبرینگ ها وسایر اجزای مکانیکی دستگاه تا حدی جلوگیری میکند همچنین مقداری هم میتوان جریان راه اندازی را کنترل کرد.
اما در اینورتر علاوه بر موارد بالا قابلیت کنترل دقیق بر روی دور موتورpid control وتوان خروجی آن ودر نهایت کنترل دبی وفشاردر خروجی دستگاه هایی مانند کمپرسور هوا را خواهیم داشت علاوه بر این کاهش قابل ملاحظه جریان راه اندازی وهمچنین بحث صرفه جویی در مصرف برق به خاطر قابلیت Energy saving اینورتر از قابلیت های آن است.
کاهش هزینه مصرف انرژی الکتریکی
در اغلب بخش های صنعتی ، انرژی الکتریکی مهمترین منبع انرژی بشمار میرود و از آنجاییکه الکتروموتورها مصرف کننده اصلی انرژی الکتریکی میباشند بهینه سازی مصرف الکتریکی از اهمیت ویژه ای برخوردار هست .
با عنایت به موضوع فوق و همچنین کاهش هزینه های تولید مشتریان خود ، استفاده از سیستم VSD ( اینورتور Variable Speed Drive ) و نصب آن برروی کمپرسور بسیار عالی است.
به تجربه ثابت شده است استفاده از VSD حدود 30 الی 35 درصد با توجه به مزایای آن هزینه مصرف انرژی الکتریکی را کاهش می دهد بطور مثال :
هزینه اولیه برای تامین یک دستگاه کمپرسور 110 کیلووات حدود 250 میلیون تومان میباشد و هزینه تامین یک دستگاه اینورتور مناسب این کمپرسور حدود 400 میلیون ریال (نوع کره ای) قیمت برق مصرفی برای 1 کیلووات ساعت مطابق تعرفه برق صنعتی اگر بطور متوسط 1500 ریال و برای این دستگاه روزانه بطور متوسط 12 ساعت کار و 300 روز در سال در نظر گرفته شود.
ریال هزینه مصرف برق 594000000=300*12*1500*110
کاهش هزینه مصرف با استفاده از VSD
178200000=30%*594000000 ملاحظه میشود که در حدود 2 سال سرمایه گذاری برای این سیستم یراحتی قابل برگشت است. و همچنین ملاحظه میشود فقط از بابت کاهش هزینه با استفاده از VSD بعد از حدود 11 سال سرمایه گذاری برای تامین یک دستگاه کمپرسور قابل برگشت است.
بدین لحاظ استفاده از اینورتور برای تولیدکنندگان توصیه میگردد و همچنین شرکت های آینده نگر مانند کارخانه های قند و فولاد – و ... استفاده از این سیستم را در سرمایه گذاری خود قرار میدهند .
برخی از مزایای استفاده از اینورتور که باعث کاهش هزینه مصرف برق به مقدار 30 ال 35 درصد می گردد:
- کاهش جریان راه اندازی موتور به مقدار حدود 20درصد که بیش از 3برابر جریان نامی موتور است بخاطر شروع سرعت موتور ازصفر
- جلوگیری از پرداخت هزینه های توان Reactive و عدم نیاز به بانک خازنی
- جلوگیری از تنشهای ناشی از استارت و استوپ های متوالی در سازه دستگاه و همچنین بلبرینگ های موتور و واحد هواساز که منجر به کاهش هزینه های تعمیر و نگهداری میگردد
- بهبود ضریب توان ( استفاده از حداکثر راندمان موتور 9 )
- جلوگیری از اختلال در شبکه و پرداخت هزینه ها از این بابت
- قابلیت برنامه ریزی متناسب با مصرف دبی و فشار هوای فشرده
- تغییر و افزایش رنج فشار و دبی بدون نیاز به تغییرات در سایز پولی
- روشن و خاموش کردن موتور بدون نیاز به کنتاکتور و تبعات ناشی از آن
- قابلیت حفاظت موتور ناشی از خطاهای الکتریکی
- جلو گیری از نشتی جریان های الکتریکی و دفرمگی های سینوسی جریان
و ...
در اینجا برخی از کاربردهای رایج برای هر کدام از آنها عبارتند از:
- سافت استارتر ها RVSS
- کاربرد هایی با گشتاور استارت کم یا متوسط
- کاربرد هایی سبکبار یا راه اندازی بدون بار No load
- عدم نیاز به کنترل سرعت موتور در حالت کار ( راه اندازی شده)
- کاهش مقداری از ضربات مکانیکی و جلوگیری محدود از صدمه استارت شدید راه اندازی به سیستم شبکه
- کنترل بخشی از جریان راه اندازی و ضربه به موتور
- کنترل و نمایش و ذخیره پارامترهای قدرت موتور و شبکه و حفاظت از موتور
- بازه پایین شیب استارت و استوپ
- اینورتر فرکانس متغیر VFD
- کنترل سرعت و قابلیت های سیستم ، داشتن حداکثر توان در سرعت های پایینVector control در طی طول کار و به صورت دائم
- برنامه های کاربردی با گشتاور استارت بالا
- فیدبک مداوم برای کنترل های خاص و دقیق مثلPID Control و Position control
- نگه داشتن روتور در سرعت صفر DC break
- از بین بردن کامل ضربات مکانیکی و جلوگیری کامل از صدمه استارت شدید راه اندازی به سیستم و موتور
- استپ و استارتهای پی درپی و مداوم.
- چپگرد و راستگرد های پی درپی و مداوم.
- بازه بسیار بالا و مطمئن و دقیق شیب راه اندازی و شیب استپ در بعضی ازمدل ها تا ۵۰۰۰ ثانیه.
- بالا بردن سرعت موتور از سرعت نامی پلاک تا ۲۰% حد مجاز.
- نصب و همسان سازی با موتورها از نظر ولتاژ و فرکانس کاری.
- دقت بسیار بالا در ولتاژ و فرکانس خروجی حتی در مواقع تعقیر ولتاژ در ورودی.
- راه اندازی موتور با باطری در مواقع خاص
- راه اندازی موتور با برق ۲ فاز در مواقع خاص
- نیازبه برنامه های کاربردی برای عملکرد های خاص و کاهش هزینه های اجرای پروژه (Multi pump -Crain-Elvator-Regenerative)
- نیاز به حفاظت های بسیار پیچیده تر و دقیق تر از موتور ماننده : خطای ولتاژ پایین شبکه – خطای
- ولتاژ بالای شبکه – خطای جریان بیش از حد موتور – خطای جریان پایین تراز حد مجاز – خطای
- دمای بیش از حد موتور -خطای دمای بالای محیط کار – خطای قطعی فاز ورودی – خطای قطعی یکی از سیم های موتورقبل از استارت و…بسیاری از خطاهای کاربردی دیگر.
اصلاح ساختار و طراحی کمپرسورهای اسکرو
برای اینکه ما قدرت و دور لازم در واحد هواساز داشته باشیم بایستی قدرت و دور را از الکتروموتور اصلی به واحد هواساز انتقال دهیم. یکی از روشهای انتقال قدرت و دوران مابین الکتروموتور و واحد هواساز انتقال به روش پولی و تسمه است.
ابتدا لازم است نگاهی کوتاه به محاسبات فنی و اینکه چه پارامترهایی در انتقال قدرت به این روش و اینکه راه کارهای ممکن جهت تغییرات در این روش و در نتیجه افزایش قابل توجه راندمان داشته باشیم.
همانطور که میدانیم برای هر ظرفیت کمپرسور یک الکتروموتور و واحد هواساز مورد نیاز است که بایستی از برندهای مشخص و جداول مربوطه که در پیوست آمده استفاده کنیم که برای مثال برای یک ظرفیت واحد هواساز و الکتروموتور انتخاب میکنیم.
فرض میکنیم پس از محاسبات مشخص میگردد ما به هوای با ظرفیت 7m3/min با فشار کاری 8.5 bar نیاز داریم.
از جدول انتخاب کمپرسورها در ستون ظرفیتها بر حسب متر مکعب بر دقیقه دنبال عدد 7 یا مقداری بیشتر میگردیم
پس از پیدا کردن این عدد میرسیم به کیلووات کمپرسور که عدد 45 کیلووات را میبینیم
فشار کاری هم 8.5 بار می باشد. (AIRMAN 60)
پس کمپرسور مورد نیاز ما یک کمپرسور 45 کیلووات با فشار کاری 8.5 بار است.
پس از به دست آوردن این مشخصات نوبت طراحی کمپرسور میرسد.
الکتروموتورهای مورد استفاده در کمپرسورها معمولا 3000RPM هستند ولی باید ببینیم چه سایز واحد هواساز و با چند دور بر دقیقه نیاز داریم.(لازم به ذکر است که محاسبات دقیق باعث راندمان بهتر دستگاه میگردد)
تمامی واحدهای هواساز مورد استفاده در کمپرسورهای اسکرو دارای گراف ها و جدولهای مخصوص خود هستند که بایستی اطلاعات اولیه مربوط به هر کدام را از آن گرافها و جداول به دست آورد.
یکی از کمپانی های معتبر سازنده این واحدها (بلوکها) شرکت معظم GARDENER DENVER است که اصالتا یک شرکت آمریکایی است و در اصل کارخانه مربوطه در کشور فنلاند قرار دارد.
با مراجعه به جدول این شرکت دنبال واحدی میگردیم که جوابگوی سایز 45 کیلووات را بدهد که در جدول با کد ENDURO12 و ENDURO25 جوابگوی این ظرفیت هستند.
پس از این مراحل باید سراغ گرافهای هر کدام برویم که تعداد دور واحد را پیدا کنیم.
اکثر این گرافها بعد از این جدول آمده است(برای مطالعه ) در گراف E12بالایی باید در خط عمودی پایینی کیلو وات مربوطه را پیدا کنیم و خط افقی را تعقیب کرده و منحنی 8.5 بار را پیدا کرده و دقیقا از آن نقطه پایین میاییم که عده ی دوران واحد را پیدا میکنیم که به عدد 6300RPM میرسیم. بعد با گراف بالایی کنترل میکنیم که آیا با این دور واحد هواساز ظرفیت مورد نیاز ما را تامین میکند یا نه.
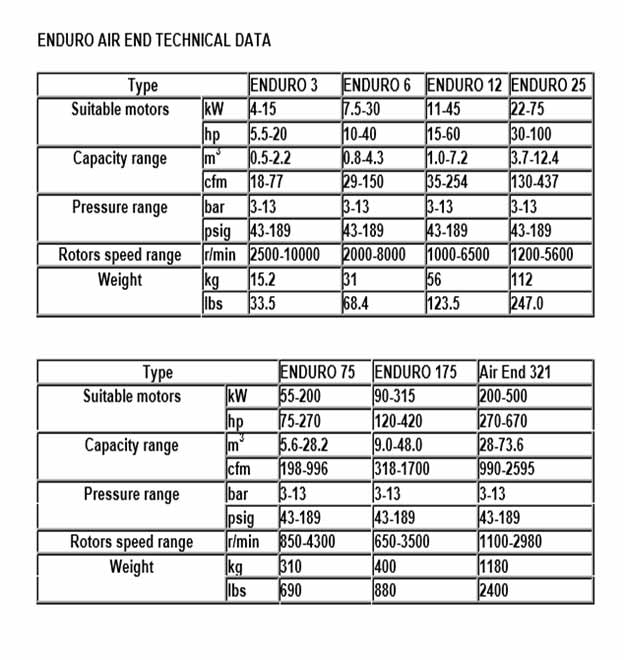
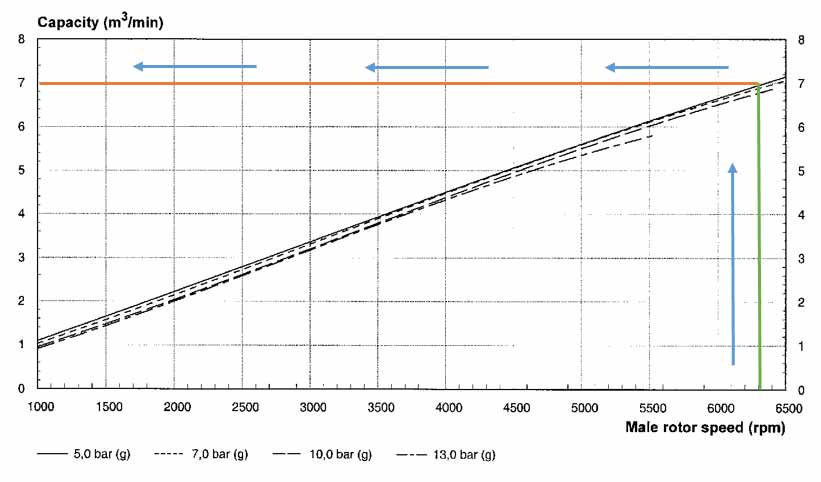
با گراف بالایی مقایسه میکنیم
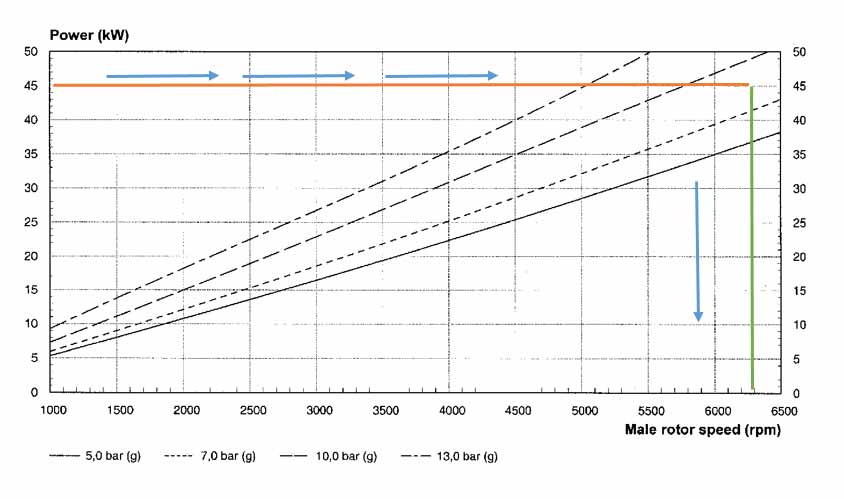
اگر الکتروموتور ما 3000RPM باشد ،بایستی واحد هواساز ما 6300 دور بر دقیقه باشد تا هوادهی لازم را داشته باشد . پس بایستی قطر پولی را باید طوری محاسبه کنیم که این تعداد دور در واحد باشد.
لازم به ذکر است قطر پولی الکتروموتور را بایستی نسبت به قطر شفت و ضخامت خار و اندازه داکتیل وسطی آن به اختیار انتخاب کنیم.
پس داریم
N1*D1=N2*D2 3000*D1=6300*D2 D2=6300÷3000D1 D2=2 1/10 D1
N1=تعداد دور الکتروموتور اصلی
N2=تعداد دور واحد هواساز
D1=قطر پولی الکتروموتور
D2= قطر پولی واحد هواساز
اگر قطر پولی الکتروموتور را 1200 میلیمتر در نظر بگیریم طبق محاسبات بالا بایستی قطر پولی واحد 2520 میلیمتر شود.
معمولا تجربه نشان داده تعداد شیارهای روی پولی با این ظرفیت کمپرسور N=4 است.
همانطور که گفتیم انتقال قدرت توسط پولی و تسمه صورت میگیرد و از طرفی دیگر گفتیم واحد هواساز بایستی به مقدار 6300 دور در دقیقه داشته باشد تا بتواند حجم 7 متر مکعب بر دقیقه را تولید کند و حتی به مقدار 100 دور بر دقیقه نیز کاهش داشته باشد مقدار هوادهی کمپرسور پایین می آید.
حال نگاه کنیم در نوع انتقال دور در سیستم پولی و تسمه چه اتفاقی می افتد.
شکل زیر شماتیکی از سیستم انتقال قدرت تسمه ایی می باشد
از پیچ تنظیم برای اعمال نیرو جهت سفت کردن تسمه استفاده می گردد.
درصورتی که اختلاف نیروی کشش تسمه بر روی تسمه موتور از نیروی اصطکاک بیشتر گردد تسمه بر روی چرخ تسمه خواهد لغزید، این پدیده را لغزش انتقالی می نامند .لغزش انتقالی همواره بر روی چرخ تسمة کوچکتر رخ می دهد و عملا ما شاهد کاهش حدودا 3% در دوران واحد هواساز هستیم. به عبارتی 189 دور کاهش داریم که یکبار دیگر اثر این کاهش دور را در چارت مربوطه مقایسه میکنیم.
همانطور که میبینیم مقدار 200 لیتر بر دقیقه کاهش حجم هوادهی داریم (خط سبز رنگ)
که به مرور زمان فرسودگی تسمه ها - خورندگی پولی ها -افزایش دمای بین تسمه و پولی بر اثر اصطکاک بر کاهش حجم هوادهی نیز کمک شایانی میکنند که تمامی این مسائل و فرسودگی سایر قطعات مکانیکی اعم از بلبرینگهای موتور و واحد هواساز و ... در این امر موثر هستند که منجر به کاهش راندمان میشوند.
همانطور که دیدیم اصطکاک بیشتر منجر به افزایش راندمان یا بهتر بگوییم باعث افزایش حداکثری انتقال قدرت الکتروموتور به واحد هواساز میشود ولی حرارت تولید شده باعث انبساط طولی تسمه شده و طبیعتا اصطکاک را کاهش داده و انتقال قدرت کاهش پیدا می کند.
یکی از راه هایی که پیشنهاد میشود در طراحی و محاسبات پولی ها در نظر گرفته شود این است که حداقل به تعداد یک شیار به تعداد شیارهای پولی ها افزوده شود به عبارتی تعداد تسمه ها افزایش یابد این امر سبب افزایش اصطکاک و جبران افت ضریب انتقال نیرو میشود و کمک شایانی به افزایش راندمان کمپرسور در بحث هوادهی می شود.
طراحی تسمه تیر کن اتوماتیک نیز کمک زیادی در این مورد می کند.